
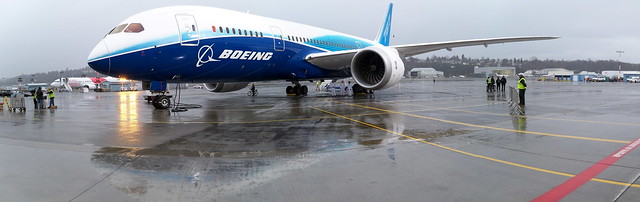
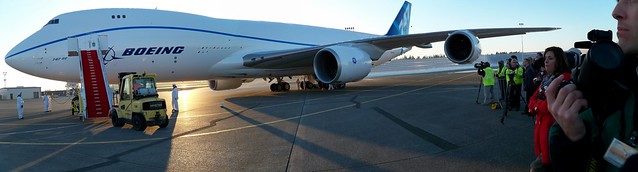
This post is an expanded version as one part of a cover story appearing in next week's issue of Flight International Magazine. See more photos from the premier of the 747-8 Intercontinental.
SEATTLE -- What originally began as a plan to sequentially develop an all-new jetliner and two jumbo variants, has turned into a concurrent push to achieve a three-front certification effort by the close of 2011.
Boeing is facing a challenge on three fronts as it aims to gain regulatory approval on the 747-8I, 747-8F and the 787 - the first time in its history it has attempted such a demanding target.
A mid-year certification for the jumbo freighter will be followed by a third-quarter sign off for 787, and closing the year with approval for the 747-8I, all while delivering a combined 25 to 40 of the new jets to Boeing's patient customers.
Boeing has never received more than two type certificates in a single calendar year, receiving regulatory approval for the 737-100 and -200 in 1967, the 757-200 and 767-200 in 1982 and 737-600 and -800 in 1998.
The 747-8I, the next program to get underway, will require a two-aircraft approximately 600h flight test campaign, set to start in 'early spring' around late March, with flight test completion in the fall, and a year-end certification, says Elizabeth Lund, 747 vice president and deputy program manager.
'The schedule is achievable, but aggressive,' says Lund, who inherited control of the 747-8 program following the ousting of Mohammed 'Mo' Yahyavi in August 2010. Pat Shanahan, serves in a dual role as 747-8 general manager, while overseeing airplane programs as vice president.
Delays on the 747-8F have stretched more than two years, with entry into service originally intended for late 2009. Manufacturing woes and flight test discoveries buckled the new freighter's schedule, as Boeing was enduring years of delays on its flagship 787, originally planned for a May 2008 first delivery.
The 747-8I, was originally slated for a 2010 first delivery, slipped as collateral damage of freighter delays, though Boeing's most recent 747-8F delay in September, held the 747-8I schedule in place for late 2011 handover to a Boeing Business Jet completion centre.
"If we have a major discovery it's always a risk in a development program, but given what we know and the learnings we've taken from the Freighter and what we've put into this program, we believe this is a schedule we can meet.
"Many of the tests we are doing on our freighter will also give us [certification] credit on the Intercontinental. We don't have to test everything from scratch," says Lund.
Already completed on the 747-8F and not required on the -8I, include the flight loads survey, artificial ice shapes testing, water spray and community noise testing, which validated that the 747-8 has a noise footprint 30% smaller than the 747-400, coming in 'quieter than we even designed,' says Lund.
Additionally, Lund says after flying a leased Korean Air 747-400 and 747-8F 'per ICAO procedures' Boeing confirmed that 'our wake vortex is exactly the same as the 747[-400]. We've submitted our data to ICAO and we're petitioning to be back in the same category as the 747-400 and 777.'
The FAA said it 'prematurely' issued a draft ruling in October 2010 on 747-8 and 787 wake clearance, increasing required spacing to 10nm, up from 4-6nm.
Still left to be completed are a variety of extreme weather tests at high winds in Keflavik, Iceland and performance evaluations at hot and high temperatures.
Boeing aims to leverage staff from across the company to assist in the flight test effort, while hiring additional personnel "to ensure we have the critical skills necessary to execute on our test commitments."
With 747-8F and 787 flight test programs ramping down "the size of test teams required for those airplanes decreases and we are able to redeploy test personnel to the 747-8I airplanes," says Boeing.
Boeing currently has 22 full-time engineering test pilots and an additional six under contract supporting commercial airplanes test programs, with a further 18 production test pilots who can assist with experimental flight test operations. Boeing has a total of 116 test pilots across its Test & Evaluation unit.
Boeing already has five 747-8F aircraft in its test fleet, along with seven 787s, potentially growing to as many as nine to support systems functionality and reliability testing.
RC001, a future Kuwaiti government aircraft, and the first of two 747-8I dedicated test aircraft, is fully instrumented and designed for flutter clearance, flight controls, ride quality, and stability and control evaluations. While RC021, which will eventually be delivered to launch customer Lufthansa, will handle much of the interiors testing of the galleys, lavatories, smoke penetration and environmental control system.
A non-instrumented third aircraft will perform electromagnetic interference testing, along with lighting and in-flight entertainment validations, while a fourth aircraft may be used for additional interiors testing, or serve as a backup if other test aircraft are in planned maintenance.
Having achieved power on in November 2010, followed by factory completion in January, Mark Feuerstein, chief 747 pilot says of RC001, "I'm a expecting a finished, tight, ready airplane to fly."
Still outstanding for Boeing is the demonstration activities to show the FAA how it intends to remedy the two biggest causes of its most recent schedule slip.
The first is the incorporation of the ouboard aileron modal suppression (OAMS) system to dampen out a 2.3-2.4Hz vibration in the wing that resulted in a deflection of ±1in (2.5cm). The vibration - or more accurately known as a limit cycle oscillation (LCO) - is virtually "imperceptible to human beings", says Feuerstein.
Todd Zarfos, 747-8 vice president of engineering, says the solution quickly revealed itself when pilots noticed that the LCO was partially alleviated when the autopilot was active. OAMS activates automatically by using the fly-by-wire outboard aileron to dampen the vibration. Using control surfaces to dampen loads is not new, as a rudder yaw damper stabilizes the aircraft in the z-axis, though this is the first time Boeing has used a roll-axis damper to eliminate a structural oscillation.
"We had long conversations with the FAA on whether existing [federal aviation regulations] covered what we were already doing. I'll just be frank, we thought they did, they characterized it as something "new and novel" and that resulted in the need for a special condition," he says.
Further, an underperforming inboard aileron actuator was replaced due to inability to handle the 3000psi hydraulic system pressure, prompting its redesign.
Zarfos says the issues were traced to pressure spikes in the hydraulic lines and he adds that engineering teams are "now in the process of correlating" the actuator underperformance and the hydraulic pressures.
Zarfos says he is "very confident" in the technical solutions to show FAA compliance, but altering the installation as the result of a kinematic evaluation of the lateral movement and wing structural dynamics.
Boeing aims to leverage staff from across the company to assist in the flight test effort, while hiring additional personnel "to ensure we have the critical skills necessary to execute on our test commitments."
With 747-8F and 787 flight test programs ramping down "the size of test teams required for those airplanes decreases and we are able to redeploy test personnel to the 747-8I airplanes," says Boeing.
Boeing currently has 22 full-time engineering test pilots and an additional six under contract supporting commercial airplanes test programs, with a further 18 production test pilots who can assist with experimental flight test operations. Boeing has a total of 116 test pilots across its Test & Evaluation unit.
Boeing already has five 747-8F aircraft in its test fleet, along with seven 787s, potentially growing to as many as nine to support systems functionality and reliability testing.
RC001, a future Kuwaiti government aircraft, and the first of two 747-8I dedicated test aircraft, is fully instrumented and designed for flutter clearance, flight controls, ride quality, and stability and control evaluations. While RC021, which will eventually be delivered to launch customer Lufthansa, will handle much of the interiors testing of the galleys, lavatories, smoke penetration and environmental control system.
A non-instrumented third aircraft will perform electromagnetic interference testing, along with lighting and in-flight entertainment validations, while a fourth aircraft may be used for additional interiors testing, or serve as a backup if other test aircraft are in planned maintenance.
One test not required for the 747-8 family is a full-scale static and fatigue test, as the fundamental three-spar architecture of the wing is unchanged from the 747-400. Only the new flight control surfaces and double-slotted inboard flap and single-slotted outboard flap require component level static testing.
Having achieved power on in November 2010, followed by factory completion in January, Mark Feuerstein, chief 747 pilot says of RC001, "I'm a expecting a finished, tight, ready airplane to fly."
Feuerstein says the systems maturity of the 747-8I revealed itself in the factory gauntlet, lasting one-quarter as long as the same set of checkouts on the 747-8F. The updated freighter designs are already evident on the Intercontinental, as both the first and second 747-8I test aircraft already sport an updated outboard landing gear door design.
Since leaving the 40-24 building after the premier celebration, Boeing has been conducting safety of flight readiness testing on RC001's fuel system. Unlike its freighter sibling, the Intercontinental features horizontal stabilizer tanks for an additional fuel capacity of 3,300gal. RC001 will soon move to the flight line for its first engine runs and the intermediate and final gauntlet tests, before conducting taxi tests just prior to its first flight in early spring.
Still outstanding for Boeing is the demonstration activities to show the FAA how it intends to remedy the two biggest causes of its most recent schedule slip.
The first is the incorporation of the ouboard aileron modal suppression (OAMS) system to dampen out a 2.3-2.4Hz vibration in the wing that resulted in a deflection of ±1in (2.5cm). The vibration - or more accurately known as a limit cycle oscillation (LCO) - is virtually "imperceptible to human beings", says Feuerstein.
Todd Zarfos, 747-8 vice president of engineering, says the solution quickly revealed itself when pilots noticed that the LCO was partially alleviated when the autopilot was active. OAMS activates automatically by using the fly-by-wire outboard aileron to dampen the vibration. Using control surfaces to dampen loads is not new, as a rudder yaw damper stabilizes the aircraft in the z-axis, though this is the first time Boeing has used a roll-axis damper to eliminate a structural oscillation.
Zarfos says the 747-8's new closed-loop roll-axis fly-by-wire came in handy for the fix, which "was very elegant and easily incorporated and it was certainly advantageous to have a fly-by-wire outboard aileron."
The aircraft's outboard aileron, in essence, acts like a noise canceling headset, delivering equal and opposite loads, nullifhttp://www.flickr.com/photos/flightblogger/5444857456/in/set-72157625921187877/ying and dampening the vibration.
'We know it'll work and now we just have to go through the last aspects of certification associated to that,' says Zarfos.
"We had long conversations with the FAA on whether existing [federal aviation regulations] covered what we were already doing. I'll just be frank, we thought they did, they characterized it as something "new and novel" and that resulted in the need for a special condition," he says.
Further, an underperforming inboard aileron actuator was replaced due to inability to handle the 3000psi hydraulic system pressure, prompting its redesign.
Zarfos says the issues were traced to pressure spikes in the hydraulic lines and he adds that engineering teams are "now in the process of correlating" the actuator underperformance and the hydraulic pressures.
Zarfos says he is "very confident" in the technical solutions to show FAA compliance, but altering the installation as the result of a kinematic evaluation of the lateral movement and wing structural dynamics.
Upon reflection of all challenges related to the flight test discoveries, Zarfos says the lack of an Iron Bird to examine the complete systems integration in a mockup before installation is one of the most important lessons learned on the 747-8.
'Clearly the lack of an intergration facility, certainly with our inboard ailerons, is a testament to that,' he says. 'On any major derivative program going forward I know certainly, I'll use the power of my office, if there is any power there, that that is one of the hallmarks. The cost trades for the good investment on the integrated facility of that nature, it is a big non-recurring cost, there is no question that the dividend that you get from that type of facility pay throughout the program.'
No comments:
Post a Comment